The main process flow of reactive printing
2022-08-10

Main process flow of reactive printing
Reactive printing is a method that uses reactive dyes to penetrate into the fabric. Reactive dye printing is the main printing process for fabrics such as cotton, linen, and silk, characterized by bright colors, comprehensive hues, good uniformity, and high dry and wet rubbing fastness. Due to the various excellent properties of reactive dyes, digital inkjet reactive printing currently occupies a significant share in the market. The main process flow of reactive printing is as follows:
1. Pre-treatment
When using reactive ink for direct printing on fabrics, it is necessary to perform a sizing treatment on the fabric (sizing → drying, with a suitable drying temperature controlled at 60 degrees). The pre-treatment plays a decisive role in the final printing effect and quality, so sufficient attention must be paid to the pre-printing process. Sizing requires the addition of sodium alginate paste, starch paste, and other pastes. To prevent some fabrics from becoming dizzy during evaporation and washing, we can also add an appropriate amount of dye-fixing salt to the paste. Since reactive dyes are under alkaline conditions, the pH value of the fabric needs to be controlled before sizing, with the paste being neutral or weakly alkaline. The main role of urea is to act as a hygroscopic agent during evaporation; controlling humidity can achieve bright colors, uniform colors, and glossy printing effects. Adjust the size formula of each component according to the influence of reactive dye ink on different fabric printing color, printing accuracy, permeability, dyeing equipment, evaporation equipment, and ink color effects.
2. Image processing
Before reactive printing, we need to separate or outline the client's draft for the inkjet image. After processing the image, we can handle it according to different images. Some images are difficult to separate, such as portraits, images with large color transitions, and rich image layers; while most digital printing patterns require color separation for printing accuracy.
3. Inkjet printing
After completing the processing of the fabric and the image, we need to lay the fabric on the printer's conveyor belt, set the corresponding printing accuracy and color curve as required, and proceed with printing. Of course, before printing, it is necessary to check whether the printer is in normal condition; if there are blockages or other issues, color performance is not acceptable.
4. Steaming
After reactive printing, the fabric is dried in a post-drying oven. The color development temperature is 102℃, steamed for 10 minutes. Follow-up for different fabric products, including fabric thickness, may vary slightly in time and need to be fine-tuned.
5. Washing
The basic process of the washing procedure is: cold water soaking → 70 ~ 80℃ hot water washing (about 10 min) → 80℃ soap washing (2 ~ 8g/L soap, 15 ~ 20 min) → 30 ~ 50℃ warm water washing → cold water rinsing. In actual operation, adjustments to the washing of printed fabrics after evaporation should be made based on the type of fabric, type of sizing, and specific requirements of the product order, including the addition of fixing agents (cationic fixing agents, crosslinking agents, etc.) and fixing agent processes.
Previous:
Related News
Contact Us
Email:
yjh@dashanyinhua.com
Telephone:
0752-6688522
Company Address:
4/F, Factory Building 1, No.2, Jinda Road, Huinan Industrial Park, Huiao Avenue, Huizhou City, Guangdong Province
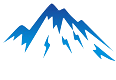
Huizhou Dashan Textile Co., Ltd
86-0752-6688522
Jiaoyuan Industrial Zone, Jiaoyuan Road, Shiwan Town, Boluo County, Huizhou City
Request a Quote
Get prices and free samples now!