Causes of Color Difference in Pure Cotton Reactive Printing and Improvement Methods
2022-06-21

Pure cotton reactive printing often uses reactive dyes to improve the first success rate of pure cotton reactive printing, control color difference within a reasonable range, and is of great significance for improving production efficiency, energy saving, emission reduction, and significantly reducing production costs. This article summarizes and analyzes the factors that easily cause color differences in the production process based on production practice, and proposes corresponding control measures. Now, let's understand the causes of color differences in pure cotton reactive printing and improvement methods!
1. Pre-treatment of pure cotton reactive printing
Only with uniform and consistent pre-treatment can pure cotton reactive printing ensure the prevention of color differences. If the pre-treatment does not meet the requirements, subsequent processing will also be difficult to achieve the expected results. Therefore, to prevent color differences, we need to start from the pre-treatment.
1. Edge sewing
The same fabric car requires sewing with the same specifications, the same manufacturer, and the same batch of fabric. If the list is too small and patchwork from different batches is needed, proper marking should be done for differentiation in subsequent processes.
2. Singeing
The singeing process generally contains a large amount of chemical glue, but if the speed suddenly slows down or the singeing flame is uneven, the fabric will be uneven when passing through the flame, leading to uneven residual glue and causing color differences. Therefore, the singeing speed must be consistent, the fabric surface must be flat, and the flame must be uniform.
3. Bleaching
During boiling, strictly control the amount of caustic soda and auxiliaries, and ensure that the steaming time, temperature, residual rate, and washing processes are stable. After boiling, thoroughly wash with water to remove residual hydrogen peroxide and avoid its retention. The width of the dry fabric should be uniform, and the moisture content should be the same.
4. Light
Strictly control the speed of the machine and the concentration of alkali, and measure the hair effect and barium value after unloading the fabric. The moisture content difference in silk fabrics should not be too large. For particularly thick fabrics, moisture in the fabric can cause uneven luster effects, leading to differences in printing results. Cotton fibers should be fully mercerized to increase the affinity of the dye for the fibers, making it less likely to migrate with moisture after adsorption, and covalently bonding with the fibers during steaming, resulting in a deeper, softer, and more uniform fabric surface.
5. Pilling
The pilling effect of the pilled fabric should be uniform. The sandpaper should not be too coarse, above 280 mesh, and during the pilling process, tension and speed need to be consistent, and the sandpaper should be replaced regularly. This is because if the pilling time is too long, the roughness of the sandpaper surface will decrease, reducing the pilling effect. Uneven pilling can lead to uneven printing colors and cause color differences.
2. Recipe and process conditions for pure cotton reactive printing
1. Materials
The reactivity of the dyes selected for pure cotton reactive printing should be moderate and similar. If the reactivity is too strong, the stability of the dye paste will be poor, especially in summer, as the storage time increases, the color of the dye paste will significantly decrease. If the reactivity is too weak, the dye cannot fully react during steaming, leading to significant color differences due to fluctuations in process conditions. When mixing colors, the reactivity of the dyes in the same formula should be as close as possible to avoid significant color changes caused by fluctuations in process conditions.
Pure cotton reactive printing should avoid using pH-sensitive dyes for color matching. For example, C.I. Reactive Black 8 (domestic Reactive Black K-BR, Reactive Black PX-N, and P-SG Black) is very sensitive to pH values, appearing red under acidic conditions and green under neutral and weak alkaline conditions. Using such dyes can easily lead to significant color differences due to slight changes in the pH of the fabric surface. Some dyes, like KN_B Black, are very sensitive to humidity during steaming. Additionally, other dyes like P-SG Black have little variation in coloring within a relative humidity range of 80%-96%, similar to the combination of Huntsman’s NC-type reactive dyes. Dyes should have good color fastness, especially good wash fastness; otherwise, the printing will not hold well after printing.
2. Sodium alginate
When sodium alginate paste contains Ca2, it combines with the alkali in the sodium alginate molecules, reducing electronegativity and weakening the electrostatic repulsion between sodium alginate and dye molecules, causing secondary mobile groups in sodium alginate molecules to react with the dye. If the amount of active dye on cotton fabric contains starch paste, the selection base of starch can also react with active dyes, reducing the color yield. Therefore, to achieve a high and stable fixation rate, sodium alginate should be selected.
3. Agents
Alkali agents provide the pH value for the reaction between active dyes and fibers during steaming. Common alkali agents are soda and pure alkali. Pure cotton reactive printing should reasonably select the type and amount of alkaline reagents based on the reactivity of the dyes. If the alkalinity is too strong, some highly reactive dye pastes will have poor storage stability, early hydrolysis due to insufficient alkalinity, and some poorly reactive dyes cannot be fully fixed on the fibers, leading to dye waste and color differences.
The above introduces the causes of color differences in pure cotton reactive printing and improvement methods. If you need to know more, feel free to contact us!
Previous:
Related News
Contact Us
Email:
yjh@dashanyinhua.com
Telephone:
0752-6688522
Company Address:
4/F, Factory Building 1, No.2, Jinda Road, Huinan Industrial Park, Huiao Avenue, Huizhou City, Guangdong Province
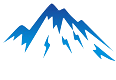
Huizhou Dashan Textile Co., Ltd
86-0752-6688522
Jiaoyuan Industrial Zone, Jiaoyuan Road, Shiwan Town, Boluo County, Huizhou City
Request a Quote
Get prices and free samples now!